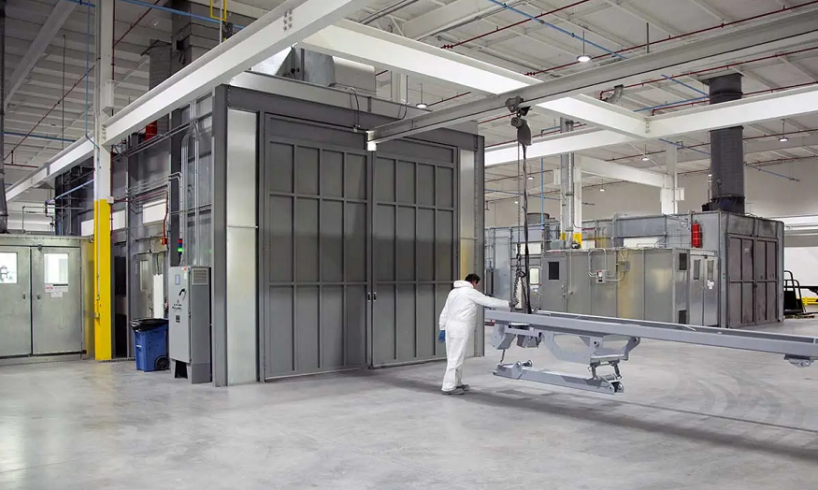
Picking the right industrial paint booth provider isn’t just about who has the best price or flashiest brochure. The right decision can make your shop more productive, while the wrong one can lead to constant breakdowns and expensive re-dos. Before signing any contracts, it helps to understand what mistakes can sneak up and cost more than you expected.
Overlooking Customizable Booth Solutions for Specialized Applications
Some projects can’t fit into a “one-size-fits-all” setup, and paint booths are no different. If the provider doesn’t offer customization—or worse, if the buyer never asks—there’s a good chance the booth won’t fully match the job it needs to do. Different industries have unique requirements: a booth designed for heavy equipment might not work well for aerospace parts or fine-detail finishing. A lack of flexibility limits productivity and slows everything down.
A good industrial paint booth should work with the process, not against it. That means custom layouts, sizes, airflow setups, and filter placements. When companies skip this and go for the default option, they often spend more later on retrofitting or troubleshooting. Choosing a provider who asks the right questions and tailors the booth to the job saves time and keeps quality consistent.
Ignoring Compliance Standards in Booth Construction Choices
Paint booths come with a long list of safety and environmental rules. These aren’t just guidelines—they’re required to keep workers safe and operations legal. Choosing a provider that overlooks national and local codes, like NFPA 33 or OSHA standards, can lead to serious trouble later. Violations may mean shutdowns, heavy fines, or worse—accidents that put workers at risk.
Beyond that, the materials used in booth construction matter. Fire-resistant panels, explosion-proof lights, and proper ventilation are all part of building a compliant industrial paint booth. Skipping out on those features might cut costs at first, but non-compliant booths can’t pass inspections or keep up with regulations. A reliable provider builds with safety and law in mind from the start, not as an afterthought.
Underestimating the Long-Term Costs of Inferior Insulation
Insulation might not be the most exciting part of a paint booth, but it plays a huge role in how efficiently it runs. Poor insulation means heat loss, slower curing times, and higher energy bills. It can also create uneven temperatures that affect finish quality. Some providers cut corners by using low-grade or thin materials that wear out faster or just don’t hold up under heavy use.
Spending a little more on well-insulated booth panels pays off quickly. It keeps the environment controlled and reduces strain on heating or curing systems. Over time, that adds up to big savings. When comparing industrial paint booth options, it’s worth asking about the insulation materials and how they perform under continuous production. A booth that holds its temperature well saves money every time it runs.
Neglecting Post-Sale Technical Support and System Integration
A booth isn’t just a metal box—it’s part of a bigger system. After installation, things can go wrong: sensors might fail, airflow might need adjusting, or the system might not connect properly with existing equipment. Choosing a provider that walks away after the sale leaves buyers scrambling for answers when problems pop up. That’s a costly headache.
Strong post-sale support means having someone to call who knows the system and can guide you through updates, fixes, or full system integration. The best industrial paint booth providers offer help with connecting curing ovens, airflow controls, and digital monitoring systems. This support keeps downtime low and productivity high. Skipping this consideration in the buying process can end up costing more than the booth itself.
Failing to Assess Provider Expertise in Advanced Curing Methods
Curing isn’t just a button you press—it’s a precise process that affects how durable and professional the final finish looks. Booths used for powder coating, UV curing, or high-temp paint systems need proper airflow, heat control, and timing functions. If a provider doesn’t understand curing science or the type of paint being used, the booth might end up delivering uneven results or slow production times.
An industrial paint booth must support consistent and even curing without overheating or cold spots. That means the provider must understand how different finishes behave and design the booth to support them. Companies that fail to ask detailed questions about curing often end up with equipment that needs major adjustments—or worse, replacement. A provider that knows the curing process from start to finish is a smart investment for long-term performance.
Choosing Budget Booths Without Considering Production Demands
Price matters, but focusing only on cost often leads to buying equipment that can’t keep up with the pace. Smaller or lower-end booths may look like a great deal, but they wear down fast under heavy production. If your shop runs large volumes or handles oversized parts, choosing a budget booth could end up bottlenecking your workflow.
It’s important to think about airflow volume, booth access, exhaust system strength, and maintenance needs. A low-cost booth that can’t handle high traffic or daily use will need more repairs and downtime, which hurts both quality and output. Investing in an industrial paint booth that matches production demands keeps projects moving and reduces frustration down the line. A booth should match the rhythm of your operation—not slow it down.